Technology-Industrial CAN Bus Solutions
Ensuring seamless integration and reliable performance
-
CAN Bus Gateways
Simplify integration with Moxa MGate secure industrial Ethernet gateways. Convert CANopen/J1939 protocols to Modbus TCP, Ethernet/IP or Profinet IO. Features intelligent diagnostics and traffic monitoring.
-
CAN Bus to Fiber Converters
Secure CAN data transmission with EMI isolation protection. Extend CAN signal transmission up to 40km via single-mode fiber connectivity. Moxa ICF converters must be deployed in pairs.
-
CAN Interface Cards
Enable seamless integration of CANbus networks into embedded systems with up to 1 Mbps speed, CAN2.0A/2.0B support, and drivers for Windows and Linux.
Solution Demo - Moxa Mgate 5121 Gateway
Connect CANOpen Device to Modbus TCP/IP network in 4 Steps
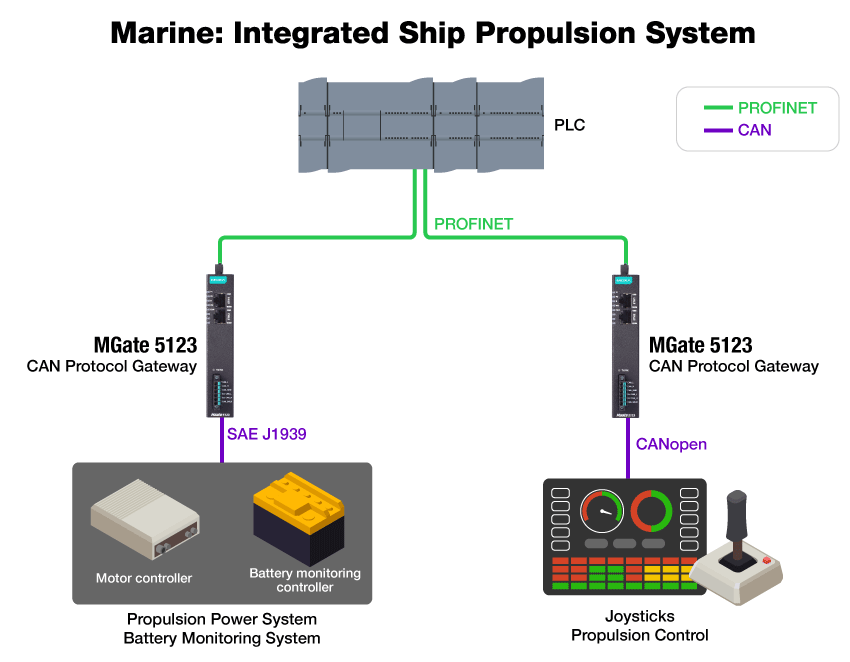
CAN Bus Protocol Gateways
System Requirement
A compact protocol gateway is needed to connect marine propulsion systems, supporting J1939 (battery), CANopen (joysticks), and PROFINET (PLC) conversions within limited cabinet space.
Solution
Moxa's compact MGate 5123 enables seamless J1939 and CANopen to PROFINET conversion with built-in diagnostics for efficient integration and troubleshoot.
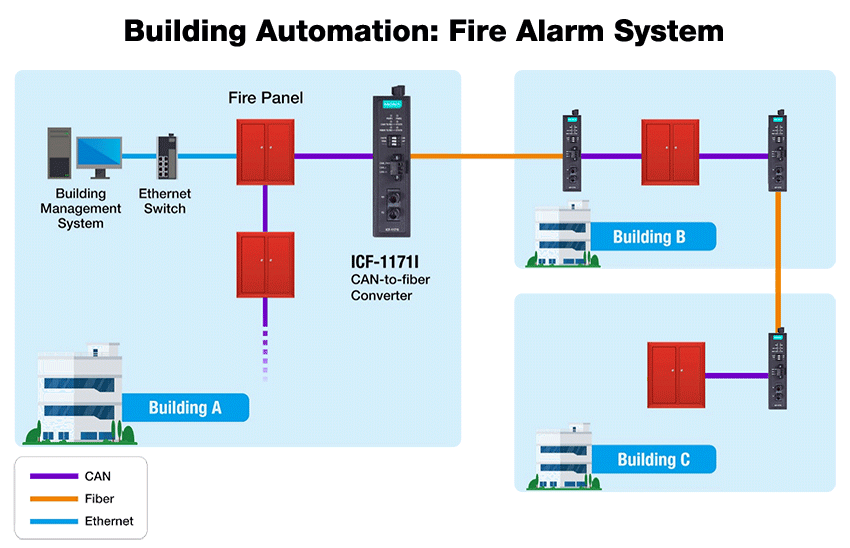
CAN to fiber Converters
System Requirement
Baud rates limit CAN bus communication distances, with higher rates reducing range. CAN to fiber converters extend communication between fire panels across buildings and must include ACK mechanism.
Solution
Moxa's ICF-1171I CAN to fiber converter supports CAN baudrate up to 1 Mbps and CAN FD baudrate up to 5 Mbps.
Fiber transmission distance can be extended up to 40 km using single-mode, or 2 km using multi-mode
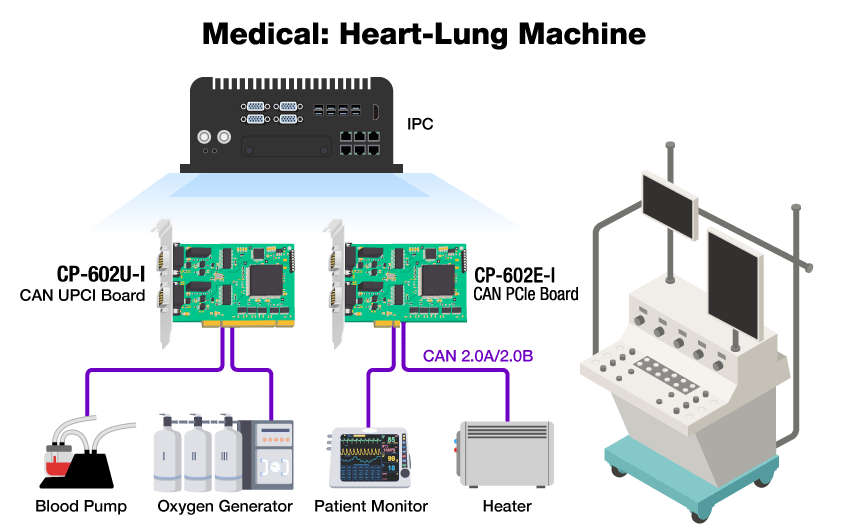
CAN Interface Cards
System Requirement
A medical component provider is designing a heart-lung machine with an Industrial PC, utilising a CAN interface for reliable communication. There is limited space and should have a modular I/O.
Solution
Moxa's CAN card easily integrates with embedded computers. Various operating systems are supported. Their drivers ensure seamless integration across both legacy and modern platforms.
Moxa Industrial CAN Bus Solutions
Contact TNS
Frequently Asked Questions
About CAN Bus Protocol
What is a CAN Bus and how does it work?
What is a CAN Bus and how does it work?
Controller Area Network (CAN) Bus is a robust, high-speed communication protocol used in industrial and automotive applications. It allows various microcontrollers and devices to communicate with each other without a host computer. The CAN Bus ensures reliable data transfer and real-time communication, making it ideal for mission-critical systems in automation, control, and machinery.
What industries use CAN Bus solutions?
What industries use CAN Bus solutions?
CAN Bus solutions are widely used in industries such as automotive, industrial automation, robotics, manufacturing, oil and gas, and transportation. These sectors rely on CAN Bus for its ability to provide real-time communication between devices and ensure high-performance, reliability, and fault tolerance in demanding environments.
System Performance
How does CAN Bus improve industrial communication?
How does CAN Bus improve industrial communication?
CAN Bus technology enhances industrial communication by enabling fast, reliable, and secure data exchange between machines, sensors, and controllers. Its decentralized architecture reduces wiring complexity, lowers costs, and improves system reliability. In industries like automation and robotics, CAN Bus ensures seamless integration and greater system scalability.
What are the advantages of using industrial-grade CAN Bus solutions?
What are the advantages of using industrial-grade CAN Bus solutions?
Industrial-grade CAN Bus solutions offer several key advantages, including:
- High reliability in harsh environments
- Real-time communication for critical systems
- Scalability to expand systems without significant reconfiguration
- Fault tolerance to ensure continuous operation even in the case of failures
These benefits make industrial CAN Bus systems ideal for demanding applications like control systems and process automation.
How do I choose the right CAN Bus solution for my application?
How do I choose the right CAN Bus solution for my application?
Choosing the right CAN Bus solution depends on factors like the specific requirements of your application, the number of devices that need to communicate, and the environment in which the system will operate. Look for solutions that offer the necessary communication speed, reliability, and scalability. Additionally, consider compatibility with your existing equipment and any necessary certifications (e.g., for industrial or hazardous environments). Consulting with an expert in industrial networking can help you select the optimal CAN Bus solution.
Why convert CAN to Fiber Optic?
Why convert CAN to Fiber Optic?
1. Immunity from electrical interference
Fiber is not affected by electromagnetic interference or radio frequency interference; consequently it provides a clean communication path and is immune to crosstalk.
2. Insulation
Optical fiber is an insulator; the glass fiber eliminates the need for using electric current as the communication medium.
3. Security
Optical fiber provides better security compared to traditional Electrical signals transmitted through a wire or radio waves Transmitted through the air. Since the light rays travel down the center of the fiber, it is extremely difficult for them to escape. In
Addition, it is nearly impossible to tap into a fiber optic cable, and Even if a tap is successful, it is possible to detect the tap by monitoring the optical power received at the termination point.
4. reliability and maintenance
Fiber is immune to adverse temperature and moisture conditions, fiber does not corrode or lose its signal, and is not affected by short circuits, Power surges, or static electricity.